Barge Drilling with the Tides
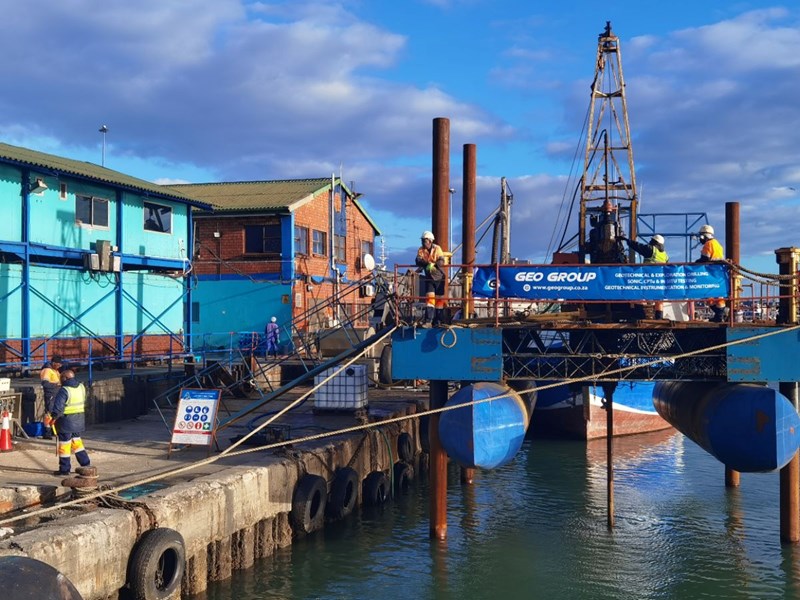
Barge drilling in tidal ports is a challenging task, but it is one that requires teamwork and perseverance. In this story, we will follow the crew of a barge drilling rig as they work to drill 12 holes in two different ports in Africa, 350 kilometres apart.
The crew faced a number of challenges, including:
The crew faced a number of challenges, including:
- Tidal ports: The tides and large swells can make it difficult to maintain a stable platform for drilling.
- Weather: Cold fronts with high winds and heavy rains can force the crew to stop work for the day.
- Communication: Good communication with the port authority is essential when planning moves around the ports and other major shipping vessels.
- Barge stability: The barge legs may sink further in or break through a harder layer, causing the barge to be off balance. The crew must level the barge before they can start drilling again.
- Drilling: Boulders collapsing the hole can make it difficult to drill to the required depth.
The crew was made up of experienced and dedicated individuals. Tyrone Stanyer, the barge skipper, oversaw the building, moving, and everyday safety on the barge. Isaac Moremi, the experienced operator, oversaw the drilling operations. These two people, plus the rest of the crew, had previous experience with barge drilling in the continent.
The crew and the two Superlink trucks, transporting the barge components, arrived at the first port to unload and begin setup of the barge at a designated slipway. Once the barge components were assembled on land, it was then pushed into the water. The barge is then moved to another docking position where the YWE-D90 drill rig and the various drilling consumables can be loaded. The team was then ready to “set sail” to the first drill position.
Once in position, the barge legs are extended for stability and drilling to commence using NWD4 casings. Each hole needed to be drilled to about 34 meters deep.
At one of the drilling locations, boulders in the seabed were causing the hole to collapse. The team had to rethink their approach and decided to telescope the boreholes starting with HW casings and drilling HQ3 to 15 meters, then telescoping the hole using NW casings and continuing drilling NQ3. Once the casing shoe had run out, they could continue drilling wireline until the NQ drill bit ran out. This proved to be a successful methodology for these collapsing holes. In addition to the telescoping approach, shorter drill runs were drilled to ensure core recovery and quality were maintained through the borehole profile.
They also had to contend with the tides and large swells. At one point, the barge legs sank further in and the barge became off balance. The crew had to quickly level the barge before they could continue drilling.
Despite the challenges, the crew persevered. They worked long hours and worked together as a team. They completed the drilling at the first port and then moved on to the second port.
Barge drilling in tidal ports is a challenging task, but it is one that can be done safely and efficiently with teamwork and perseverance. The crew of the barge drilling rig in this story demonstrated these qualities. They overcame every challenge they faced and completed the project on time.
The GeoGroup “Jack-tup” Barge is SAMSA (South African Maritime Safety Authority) registered for inland water that includes ports and estuaries, dams, and rivers.
The crew and the two Superlink trucks, transporting the barge components, arrived at the first port to unload and begin setup of the barge at a designated slipway. Once the barge components were assembled on land, it was then pushed into the water. The barge is then moved to another docking position where the YWE-D90 drill rig and the various drilling consumables can be loaded. The team was then ready to “set sail” to the first drill position.
Once in position, the barge legs are extended for stability and drilling to commence using NWD4 casings. Each hole needed to be drilled to about 34 meters deep.
At one of the drilling locations, boulders in the seabed were causing the hole to collapse. The team had to rethink their approach and decided to telescope the boreholes starting with HW casings and drilling HQ3 to 15 meters, then telescoping the hole using NW casings and continuing drilling NQ3. Once the casing shoe had run out, they could continue drilling wireline until the NQ drill bit ran out. This proved to be a successful methodology for these collapsing holes. In addition to the telescoping approach, shorter drill runs were drilled to ensure core recovery and quality were maintained through the borehole profile.
They also had to contend with the tides and large swells. At one point, the barge legs sank further in and the barge became off balance. The crew had to quickly level the barge before they could continue drilling.
Despite the challenges, the crew persevered. They worked long hours and worked together as a team. They completed the drilling at the first port and then moved on to the second port.
Barge drilling in tidal ports is a challenging task, but it is one that can be done safely and efficiently with teamwork and perseverance. The crew of the barge drilling rig in this story demonstrated these qualities. They overcame every challenge they faced and completed the project on time.
The GeoGroup “Jack-tup” Barge is SAMSA (South African Maritime Safety Authority) registered for inland water that includes ports and estuaries, dams, and rivers.
Plot 28 Central Road
Sunrella, Lanseria
Gauteng
South Africa
Tel. +27 (0)11 966 7760
Fax. +27 (0)86 663 3896
Email. info@geogroup.co.za