Drilling to Source Stone for Road Maintenance
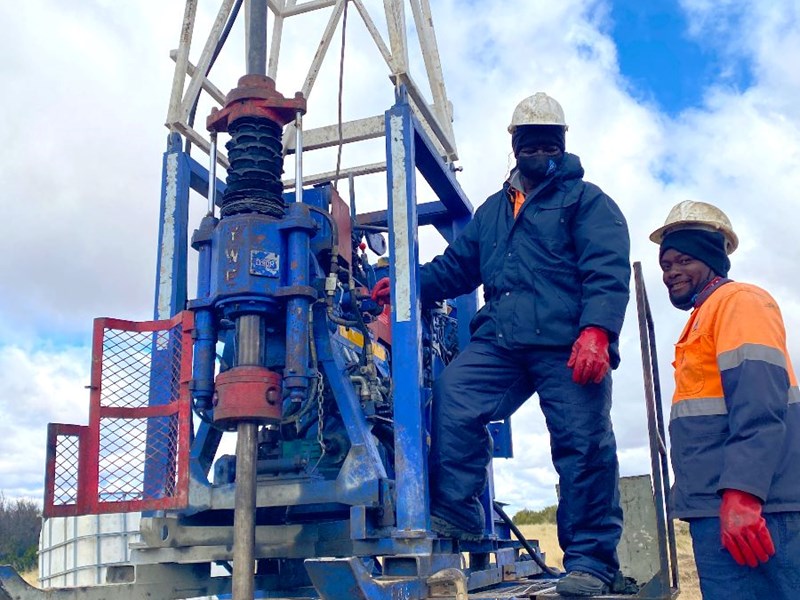
In December 2021, the Geomech Africa team broke ground in the Free State province in South Africa to conduct Geotechnical Investigations as part of a 2-phase plan to drill for the discovery of quarry materials. These materials are to be used for the construction of new roads and the maintenance and repair of the existing roadway infrastructure.
Project manager for the GeoGroup, Lans Schick, was appointed to manage 18 drill rigs (16 rotary core drills and 2 percussion rigs) and the drill teams in terms of logistics, planning and production. As challenging as this task seemed, Lans and his team were fully committed to seeing it through to the end.
The original scope of work for the project required the Geomech Africa team to drill a scope of holes at 55 various locations throughout the province and needed to be completed within one year. The project was divided into two phases to ensure the effective sourcing of materials within the given timeframe. The first phase entailed percussion drilling to 30 meters at each of the 30 holes. This allowed them to determine the narrowing of the area for material sourcing after which the second phase of drilling can begin. The second phase required rotary core drilling up to 25-meter depths at a total of 25 holes at each site. “The region of farms where we were required to source the material from extended from Koppas in the north to Smithfield in the south and then from Harry Smith in the east to Polokwane in the west.” Lans added.
A total of 25 050 percussion meters were drilled and a total of 10 883m were drilled rotary core.
As with many projects, it’s inevitable that our teams would face unforeseen challenges. For the most part, the team had to prepare themselves for the various challenging climate and terrain conditions that awaited them. With extreme heat in the summers and below freezing temps in the winters. All the necessary plans had to be made to ensure the safety and comfort of the crews by providing them with all the appropriate gear. The rainy season also created challenges as the wet conditions created muddy ground conditions causing access issues. Luckily, the team were equipped with 4x4 vehicles, trucks and TLB’s that assisted the rigs in the harder-to-reach locations.
For a project of this size and with the scheduled amount of drill locations, it was important to have all the logistical plans in place to ensure that all the staff were ready to move accommodation sites as soon as they finish in a specific area. This required our office team to constantly be in touch with the project manager to ensure that all the accommodation arrangements were made in order for the teams to arrive and check in on time to avoid any delays. With remote sites, it was always necessary for the various business divisions to ensure that water and fuel were readily available to avoid any delays to the drilling schedule.
The Free State is well-known as an agricultural hub. This meant that the GeoGroup teams had to take extra precautions when it came to the environment. Our teams had to ensure minimal impact to the environment and that drill sites were rehabilitated before deploying to the next destination. Wherever drilling took place on farmlands, the farmer would need to present the GeoGroup with a site clearance certificate to validate that the farmer was pleased with how the site was left after operations were completed.
At the end of the project, the crews were able to complete all the drilling 30 days earlier than anticipated and drilled more than 35 000 meters using a combination of percussion and rotary core drill rigs.
“The successful execution and timeous completion of the project would never have been possible without a top-notch and highly experienced drilling staff. The crews were always prepared to go the extra mile and stay motivated through some difficult and challenging times.” - Lans Schick
Plot 28 Central Road
Sunrella, Lanseria
Gauteng
South Africa
Tel. +27 (0)11 966 7760
Fax. +27 (0)86 663 3896
Email. info@geogroup.co.za